Xylar Coated Fasteners
XYLAR® coatings manufactured by Whitford® Corporation have an inorganic, ceramic-metallic bonding agent rather than the organic polymer resin used in XYLAN® coatings. The ceramic-metallic “cornerstone” creates coatings which are much harder
than their organic counterparts and have the potential for much higher operating temperatures, depending upon the fillers and additives selected for use in the coating. They provide exceptional thin-film corrosion protection and are often top-coated
with one of the lubricated XYLAN® coatings.
XYLAR® coatings can also be used alone when a lubricated surface is not needed. XYLAR® coatings are recommended for use in three major application areas: protecting metal from oxidation due to water in all forms: sea water, ice, steam,
even subterranean condensation; protecting metal from high temperature oxidation up to 1000F (535C); providing a sacrificial primer for any conventional air sprayed lubricating coating.
Xylar 2 is a water and solvent based product. A slightly different chemical composition to Xylar 1, although it remains a “cermet”. This modification produces a coating which is easier and more forgiving to apply. Xylar coatings provide
the aerospace and marine industries with materials to protect components from high temperature, oxidization, salt laden atmospheres, chemicals and abrasives.
- Xylar® 1 - Aqueous/Acidic Base aluminium Cermet coating which provides excellent chemical & corrosion as well as abrasion resistance at elevated temperatures.
- Xylar 2 - Xylar® 2 is the cornerstone of a generation of hard, cermet finishes that offers a tough, sacrificial barrier to corrosion and wear. Xylar 101
- Xylar® 101 - is a sealer/topcoat that enhances the corrosion resistance of Xylar® 2. It is a dense, clear film that fills any surface pores on Xylar® 2 and together they represent a breakthrough in coating technology - a thin-film barrier with
extreme corrosion resistance.
- Xylar 101 - Xylar® 101 is a dry-film lubricant with a friction coefficient of approximately 0.06. Used by itself, Xylar® 201 provides the slickest dry-lubricating surface available. As a topcoat with Xylar® 2, it provides both low friction and
extreme wear resistance.
- Controlled torque : Low co-efficient of friction coatings, reducing and improving the uniformity of make-up torque.
- Corrosion resistance : 500 to <5000 hours corrosion performance can be achieved - reliant on the correct pre-treatment and application of the primer and/or topcoat system.
- Chemical resistance : Excellent resistance to many of the chemicals and fluids used in the Oil & Gas sector.
- Heat resistance : Wide continuous use temperatures of fluoropolymer topcoats. Xylar primers can achieve up to +535°C.
- Abrasion resistance : Hard-wearing, low coefficient of friction coatings ideal for fastener applications.
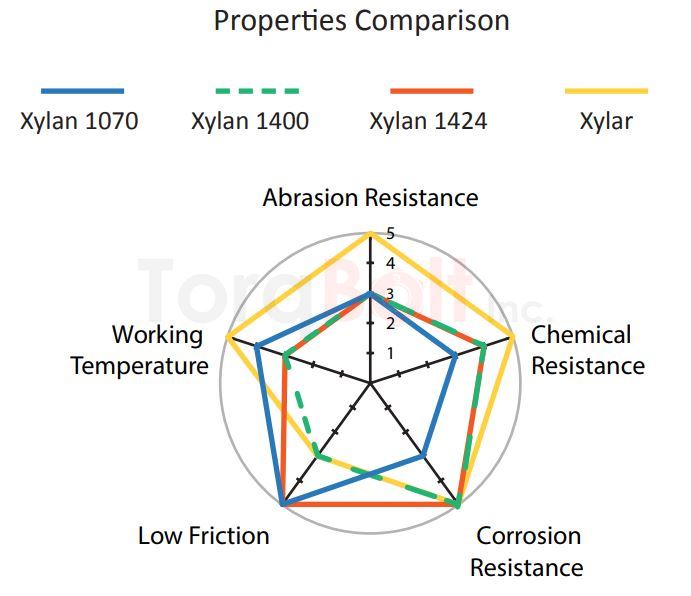
Xylan 1070 vs 1400 vs 1424 vs XYLAR
Topcoats can be used with a variety of pre-treatments and primers to achieve varying levels of corrosion performance <5000 hours ASTM B117 salt spray resistance.
- Xylan 1070 : Organic solvent based, low friction coating for fasteners. Normally used over a range of pre-treatments or primers which can provide over 5000 hours of salt spray resistance.
- Xylan 1400 : Organic solvent based, tough coating offering excellent protection against corrosion caused by road salt, acid rain and other forms of environmental corrosion.
- Xylan 1424 : Aqueous based, resin bonded dry film lubricant coating primarily formulated to prevent corrosion and facilitate make-up torque on fasteners.
- Xylan : A range of ceramic metallic coatings which provide superb corrosion performance and excellent chemical and abrasion resistance at extreme temperature
Product |
Zn Phos. |
Zn Plate |
Zn Ni Plate |
Xylar* |
Xylan 1070 |
>500hrs |
>1500hrs |
>3000hrs |
>5000hrs |
Xylan 1400 |
>1500hrs |
>2500hrs |
>4000hrs |
>5000hrs |
Xylan 1424 |
>1500hrs |
>2500hrs |
>4000hrs |
>5000hrs |
For application follow Whitford guidelines - use a capable or Whitford recommended applicator *Data based on 0%RR (Industry standard failure = 15%RR)
Test |
ASTM |
Xylan 1070 |
Xylan 1400 |
Xylan 1424 |
Xylar |
Dry-Film Thickness |
D1186 |
15-25 µm / 0.6-1.0 mils |
Adhesion |
D3359 |
>3B |
>3B |
>3B |
>3B |
Film Hardness |
D3363 |
2H - 4H |
2H - 3H |
2H - 3H |
>3H |
Coefficient of Friction |
G99 |
0.05 to 0.12 |
- |
0.05 to 0.09 |
0.11 to 0.13 |
Working Temp. Range |
- |
-195°C to +260°C |
-50°C to +190°C |
-50°C to +175°C |
-40°C to +535°C |
Impact |
D2794 |
Pass |
Pass |
Pass |
N/A |
- Xylar 1 coatings provide the aircraft, aerospace and marine industries with materials to protect components from high temperature oxidation, salt laden atmospheres, chemicals and abrasives.
- Xylar 2 is typically applied to aerospace and marine industry components. This product is also used as a thermal barrier for automotive engine and exhaust components.
- Xylan® dry-film lubricatiing coatings provide a wide range of functional attributes which are ideally suited to fastener applications in the energy, petrochemical & water treatment industries.
- Xylar® 2 gives 300 to 400 hours of salt fog protection, or about 6,000 hours of protection when topcoated with Xylar® 101. Recommended applications include pump impellers, turbine blades compressor housings, valve bodies, agitators, petrochemical reactor parts, paper machine components, exhaust stacks, marine hardware, equipment used in photo processing, or other parts that need thin film protection - at temperatures all the way up to 1,200°F/650°C.
- Xylar® 2 and 2/101 are used to separate dissim- ilar metals in engine/generator applications, sus- pension mounts, air cylinders, electrical controls, industrial brakes and clutches, air pumps, reels, materials-handling equipment, industrial ovens, tubing systems, gear reducers, ball screws, governor systems, motor housing, and literally hundreds of other applications - at ambient or extreme temperatures.
- Xylar® 2 is used in abrasive applications such as furnace chutes, air ducts, grain-handling equip- ment, and numerous vehicle-underbody compo- nents where abrasive wear or stone pecking is common. The combination of Xylar® 2/201 is pre- ferred for applications where parts wear against each other, or where parts are dragged over abrasive media.
- Xylar® 2/101 performs better than any existing dry-film lubricating coating in bearing and wear applications such as power screws, gears, com- pressor rotors, clutch actuators, slides, and valves. It is also an excellent coating to use in lightly loaded conditions where "stick-slip" is a problem. Examples include handbrake compo- nents where aluminum slides against aluminum or stainless slides against stainless.
- Extreme temperature resistant
- Abrasion/wear resistant
- High corrosion resistance
- Provides sacrificial anodic protection
- Thermoset
- Colours available : Dull grey/silver when burnished
- Abrasion resistance : Very good
- Chemical resistance : Good
- Corrosion resistance : Excellent
- Cure temperature MAX [PMT] : 15 mins @ 400°C/750°F
- Cure temperature min [PMT] : 30 mins @ 343°C/650°F
- Working temperature, range (continuous) : -40°C/-40°F to 535°C/995°F
- Film thickness : 15-30 microns
Xylar® 2 and 2/101 are the building blocks to corrosion protection. Xylar® 2 is a porous ceramic coating that is extremely hard and, with respect to structural metals, is chemically sacrificial. Applied to ferrous, aluminum, or other metals, it is
"sacri- ficed" to a corrosive medium before the substrate is attacked. Xylar® 101 is a sealer/topcoat that closes any surface pores of Xylar® 2. The 1 to 1.5 mil (0.0254 to 0.0381 mm) combination provides an incredible 4,000+ hours of protection
in ASTM B117 salt fog tests
Xylar® 2 cermet coating breaks the electrical path between dissimilar metal parts. It is hard (8H), simple to apply, and because it is so thin (1 to 1.5 mils) it does not interfere with most component tolerances. The high temperature stability of
Xylar® 2 (1,200°F/650°C) makes it ideal for engine applications where the electrical couple between dissimilar metals could result in corrosion.
Xylar® 2 is used in abrasive applications such as furnace chutes, air ducts, grain-handling equipment, and numerous vehicle-underbody components where abrasive wear or stone pecking is common. The combination of Xylar® 2/201 is preferred for
applications where parts wear against each other, or where parts are dragged over abrasive media.
Xylar® 2/101 performs better than any existing dry-film lubricating coating in bearing and wear applications such as power screws, gears, compressor rotors, clutch actuators, slides, and valves. It is also an excellent coating to use in lightly
loaded conditions where "stick-slip" is a problem. Examples include handbrake components where aluminum slides against aluminum or stainless slides against stainless.